

I also don't know why hsm for solidworks has other features such as axis substitution that would be vital for our work. However absolutely none of it for inventor cam customers. I've seen some improvements for fusion lately online that developers are finishing up 4 axis 3D machining. However the lack of multi axis support is astonishing. Programming a part in inventor cam that requires 3 axis work is great. When that happens, the machine must pause after each move and wait for the next servo command from the control.We picked up inventor cam for one reason and one reason only: its cheaper than esprit for simple parts. Short line moves and high feedrates can force the processing rate beyond what the control can handle. That can be as few as 40 blocks/second on older machines and 1,000 blocks/second or more on a newer machine like the Haas Automation control.
#Inventorcam xyz not ijk code#
CNC controls can only process a finite number of lines of code (blocks) per second. However, short line moves, coupled with high feedrates, may result in a phenomenon known as data starving.ĭata starving occurs when the control becomes so overwhelmed with data that it cannot keep up. The first two are not much of a problem because Inventor CAM calculates very quickly and most modern controls have at least 1MB of RAM. It is tempting to always use very tight tolerances, but there are trade-offs including longer toolpath calculation times, large G-code files, and very short line moves. More lines result in a toolpath that more closely approximates the nominal shape of the spline or surface. How accurately the toolpath matches the desired shape depends largely on the number of lines used. To accommodate this, CAM approximates spline and surface toolpaths by linearizing them creating many short line segments to approximate the desired shape. Model box point - Select a point on the model bounding box for the triad origin.ĬNC machine contouring motion is controlled using line G1 and arc G2 G3 commands.Stock box point - Select a point on the stock bounding box for the triad origin.Selected point - Select a vertex or an edge for the triad origin.Model origin - Uses the coordinate system (WCS) origin of the current part for the tool origin.Setup WCS origin - Uses the workpiece coordinate system (WCS) origin of the current setup for the tool origin.The Origin drop-down menu offers the following options for locating the triad origin: Use this if your model does not contain a suitable point & plane for your operation.
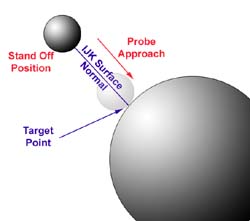
This uses both the origin and orientation of the existing coordinate system. Select coordinate system - Sets a specific tool orientation for this operation from a defined user coordinate system in the model.Both the X and Y axes can be flipped 180 degrees. Select X & Y axes - Select a face or an edge to define the X axis and another face or edge to define the Y axis.Both the Z and Y axes can be flipped 180 degrees. Select Z axis/plane & Y axis - Select a face or an edge to define the Z axis and another face or edge to define the Y axis.Both the Z and X axes can be flipped 180 degrees. Select Z axis/plane & X axis - Select a face or an edge to define the Z axis and another face or edge to define the X axis.Model orientation - Uses the coordinate system (WCS) of the current part for the tool orientation.Setup WCS orientation - Uses the workpiece coordinate system (WCS) of the current setup for the tool orientation.The Orientation drop-down menu provides the following options to set the orientation of the X, Y, and Z triad axes: Specifies how the tool orientation is determined using a combination of triad orientation and origin options.
